- Home
- EN
- Kardham Group
- News
How Kardham Architects are rethinking buildings in light of new environmental demands
May 2021
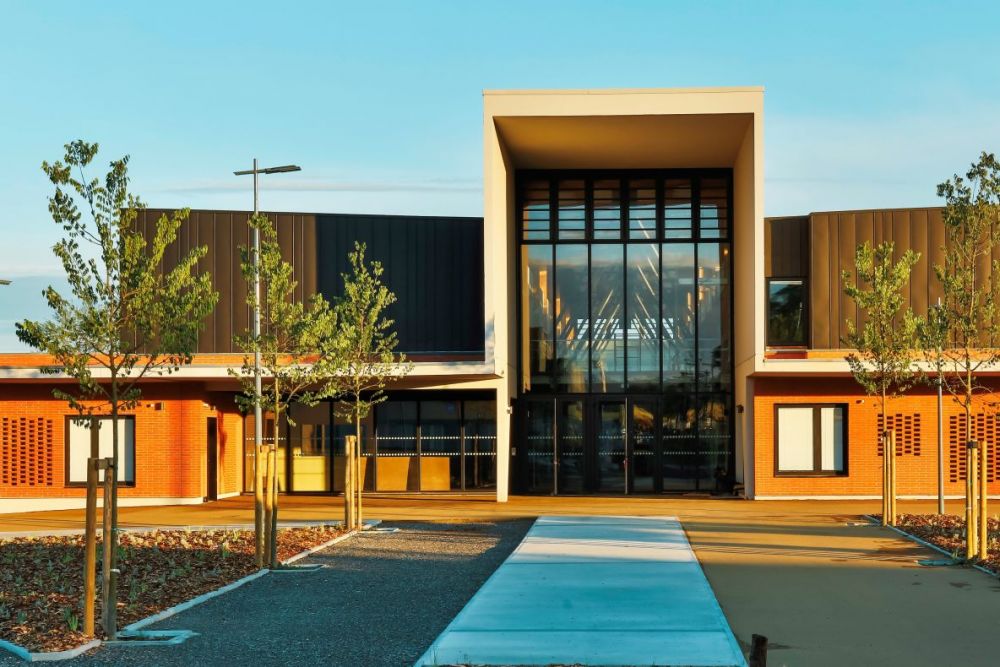
As the entry into force of RE2020 approaches, the architecture and design firm Kardham is increasing the proportion of bio-based materials in its projects. Difficulties remain latent on certain elements, such as the cost of French stone or the insulation of thermal strainers, a "futile campaign" if the materials are poorly chosen.
Interview with David Habrias, CEO of the Kardham Group, published in L'Usine Nouvelle in April 2021.
From January 2022, the launch, in successive phases, of the new RE2020 environmental regulations will induce profound changes in the design of buildings. “The government belatedly changed the way of calculating life cycle analysis, which now overvalues biobased materials, which was not the case before and which is not the method of calculation of other European countries.”, Comments David Habrias, managing director of the Kardham group, in charge of architecture. In the previous calculation method, 1 cubic meter of wood weighed 100kg of CO2. In the new calculation method, 1 cubic meter of wood has a negative value and weighs -250kg of CO2”.
With a head office in Paris, Kardham (400 people, 72.5 million euros in turnover) provides intellectual services (consulting, architecture, engineering, space design, digital) in the building sector and of real estate. To integrate the requirements of RE2020 and the challenges linked to climate change, he advocates "constructive biodiversity": "we must be able to find the right solutions according to the criteria we wish to address. We must also take into account the evolution of building uses".
Thinner frames of buildings are drawn. "Mixed structures are starting to become commonplace, but in France, the culture of concrete remains strong." Depending on the project, more space is given to other materials, such as stone, which is currently recording strong sales growth. "If there is a slight additional cost of French stone compared to imported stone, it remains contained since the stone will represent 3% or 4% of the overall cost of a building, and we can justify an overquality local materials, ” adds David Habrias, who prefers to focus on made in France. On wood, the place of which will mechanically progress in construction, he estimates the time allowed between thirty and forty years to apprehend the end of life of the structures and find solutions for recovery.
Composite materials difficult to deploy.
“The campaign to insulate from the outside against thermal strainers is futile: you never recover the carbon from the materials in saving heating.“
Beyond materials, adaptation to change also involves insulation. "For a very long time, the designers worked a lot on the envelope, and over-insulated buildings. The whole campaign of insulation from the outside against thermal strainers is in vain: you never recover carbon in heating savings , lower than the carbon cost of manufacturing insulation. This applies to all buildings", slice David Habrias, whose company specializes in large equipment (stadiums, hospitals, etc.)
To see new avenues, Kardham is currently carrying out experiments in 3D printing, with the Ecole des Ponts. "By adding a small percentage of fibers in the concrete, we can improve its tensile performance by 20 to 40 times", explains the manager. However, this type of composite material is now considered in Eurocodes 6 (masonry), whereas a wider application in the building would require moving towards Eurocodes 2 (shell). These European standards relate to the dimensioning of building and civil engineering structures. Another observation: the “not so simple” implementation of so-called “low carbon” concretes, due to longer setting times.