- Home
- EN
- Our impact
- ProspeKtive
- Offsite will not happen without a profound digital and cultural transformation
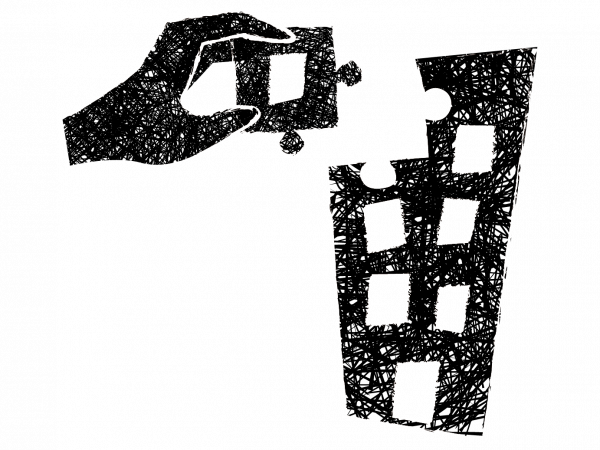
Offsite will not happen without a profound digital and cultural transformation
May 2024
Expert
Let's be clear: the often-used term "real estate industry" has never been more irrelevant. Despite technological advances, many projects are still being developed in the traditional way, using unsuitable or even obsolete tools. In the light of growing economic and environmental demands, off-site construction could provide our industry with a lever for industrialization and modernization. A way to build faster, better and cheaper. Provided we encourage innovation and a genuine culture of change.
Impact, deadlines, costs, quality: off-site is good for everything!
The industrialization of the construction industry is not a new phenomenon. At the end of the Second World War, the use of prefabrication made it possible to rebuild a ravaged country faster, at lower cost and without the necessary skilled labor. But it's only in recent years that off-site construction has been gaining ground, driven in particular by the real estate industry's pressing need to embrace circular economy in a world where resources are increasingly limited. Off-site construction offers a number of ecological advantages, particularly in terms of waste reduction.
By prefabricating building elements to precise specifications in the factory, then assembling them like a set of LEGO® on the building site, it minimizes material waste on the building site, thus limiting the environmental impact of projects. Another advantage: by manufacturing the building elements in the factory simultaneously with site preparation, the process considerably reduces construction times. And time is money: the standardization of manufacturing processes and the reduction of material waste contribute to better control of construction costs. Quality is not forgotten either. The controlled conditions of the industrial environment guarantee consistently high quality of prefabricated building components, and mass production minimizes human error and construction defects. Ultimately, by moving part of the construction process to the factory, greater precision and standardization of processes is achieved, and thus greater overall project performance.
- No off-site without BIM
There are still a number of obstacles to the adoption of off-site construction. The first is a digital culture - and in particular a BIM (Building Information Modeling) approach - that is still underdeveloped in project design. Yet BIM - a working method that uses an intelligent 3D digital model as the central element of exchanges between the various parties involved in the act of building - and off-site construction reinforce each other by providing tools and processes to design, manufacture and construct buildings more efficiently and sustainably. By displacing factory-based construction, off-site requires maximum precision and consistency, and therefore a BIM approach to better modeling of building elements designed and manufactured using 3D digital models.
Off-site also implies efficient management of building-related data - dimensions, materials, costs, deadlines, etc. - which is essential for optimal planning, design and manufacture of building components. - essential for planning, designing and manufacturing building components in the best possible way. So, while prefabrication of building components reduces risks and delays on site by manufacturing components in a controlled environment, it is BIM that will optimize the construction process, right from the earliest stages of design. As you can see, greater use of offsite will not be possible without the parallel use of BIM. This is far from being the case: despite the 2015 Plan de Transition Numérique dans le Bâtiment and the Plan BIM 2022, both of which aim to generalize the use of BIM, it has to be said that, to date, only 35% to 50% of professionals in the sector use it*.
- Promoting a culture of change
Furthermore, promoting the use of off-site construction implies a significant change in working methods, and professionals may be reluctant to abandon construction processes to which they are accustomed in favor of new approaches. This cultural barrier is all the more real given that, despite its advantages, off-site construction can sometimes be perceived as a lower-quality or less personalized option than on-site construction. Enhancing the image of off-site construction, and convincing customers and stakeholders of the quality and reliability of our projects, is a major challenge.
And project owners - together with their contractors and specifiers, project management assistants and architects - play a decisive role in raising awareness. By forcing greater adoption of digital technology, and BIM design in particular, and promoting offsite in their projects, they can stimulate innovation and encourage market players to adopt more modern, efficient practices. As usage is often the driving force behind any change, greater demand for off-site construction could remove another brake: that of the wallet. As far as manufacturers and industrialists are concerned, setting up in-plant production facilities and acquiring specialized equipment requires a substantial initial investment, and can be a major obstacle to the expansion of this constructive process. Better visibility of demand would also enable them to perfect or develop new offers.
Off-site construction and renovation can be a lever for industrializing our industry, which needs processes more than ever to meet urgent economic and ecological needs. The mobilization of public and semi-public contracting authorities is essential. A charter for the development of off-site construction and an association of French off-site players have already been created, signs of a mobilization that is only waiting to grow. But there's still a long way to go. While the third Annual Off-Site Barometer shows that 44% of professionals have already implemented off-site construction by 2023, an increase of 13 points on the previous edition**, the fact remains that until recently, off-site construction represented just 1% of construction in France***.
References
- *Source Revizto
- **Baromètre Batimat, Campus Hors-Site et ACIM
- ***Rapport Michel-Rivaton sur l’industrialisation de la construction, janvier 2021
Release date: May 2024